Delivering Value at Scale
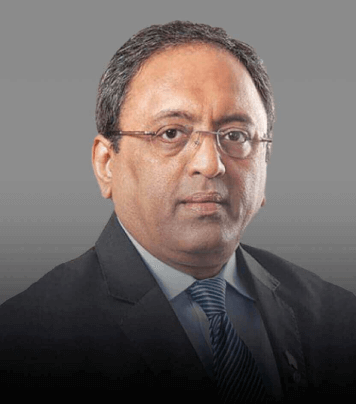
We are grateful to the authorities for the swift passage of the proposed transaction through statutory processes and for its approval in a record time. This integration is much more than just the coming together of two highly successful companies. It is about turning the collective wisdom of the two companies into a much larger force for creating long-term value for all our stakeholders.
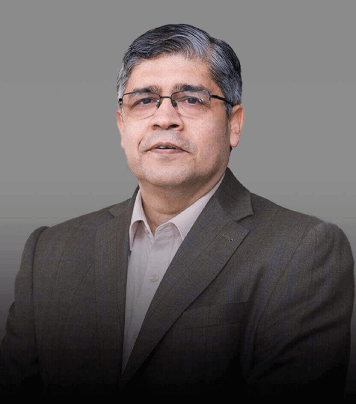
Amid the proliferation of new business models and revenue streams in a rapidly converging world, LTIMindtree will help businesses proactively take on and shape the future by harnessing the full power of digital technologies. Armed with top talent, comprehensive offerings, and a cumulative experience of more than five decades, LTIMindtree brings the diversity of scale and capabilities required to help businesses reimagine possibilities, deliver impact, and get to the future, faster.
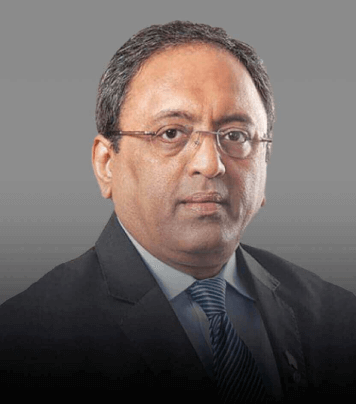
We are grateful to the authorities for the swift passage of the proposed transaction through statutory processes and for its approval in a record time. This integration is much more than just the coming together of two highly successful companies. It is about turning the collective wisdom of the two companies into a much larger force for creating long-term value for all our stakeholders.
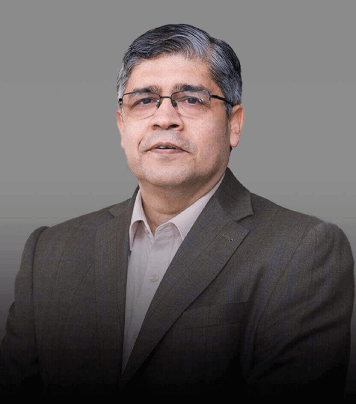
Amid the proliferation of new business models and revenue streams in a rapidly converging world, LTIMindtree will help businesses proactively take on and shape the future by harnessing the full power of digital technologies. Armed with top talent, comprehensive offerings, and a cumulative experience of more than five decades, LTIMindtree brings the diversity of scale and capabilities required to help businesses reimagine possibilities, deliver impact, and get to the future, faster.
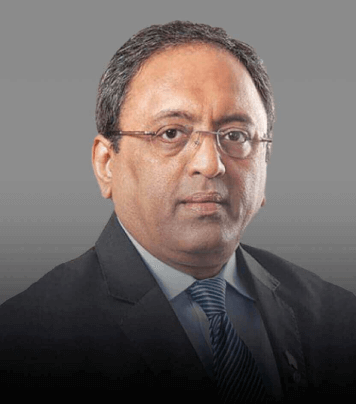
We are grateful to the authorities for the swift passage of the proposed transaction through statutory processes and for its approval in a record time. This integration is much more than just the coming together of two highly successful companies. It is about turning the collective wisdom of the two companies into a much larger force for creating long-term value for all our stakeholders.
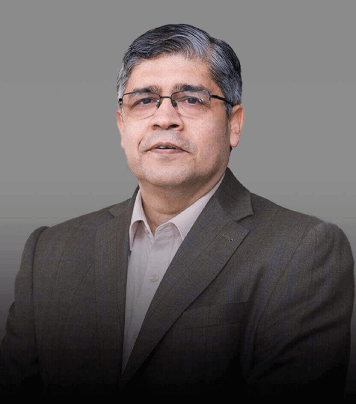
Amid the proliferation of new business models and revenue streams in a rapidly converging world, LTIMindtree will help businesses proactively take on and shape the future by harnessing the full power of digital technologies. Armed with top talent, comprehensive offerings, and a cumulative experience of more than five decades, LTIMindtree brings the diversity of scale and capabilities required to help businesses reimagine possibilities, deliver impact, and get to the future, faster.
Creating Next Level Growth
Revenue
Clients
Employees
Countries
Unmatched Core to Experience Transformation
LTIMindtree is a new kind of technology consulting company. We help businesses transform – from core to experience – to thrive in the marketplace of the future. With a unique blend of the engineering DNA with experience DNA, LTIMindtree helps businesses get to the future, faster.
Together Creating Value
Services
Partners
Client Speak
LTIMindtree played a pivotal role in Gen Re's cloud migration journey, addressing scale challenges and geographic diversity with a highly skilled team. Their comprehensive approach ensured a seamless transition, meeting Gen Re's objectives successfully. Erik Kasir, VP at Gen Re, commended LTIMindtree for their strategic selection, effective risk mitigation, and collaborative teamwork.
Johan Gabrielsson, Head of Digital Products & Services at OKQ8, talks about their long-lasting partnership with LTIMindtree in Digital Products & Platforms. The association has expanded from early IT development to creating innovative apps for sustainable mobility. OKQ8 and LTIMindtree's partnership has now shifted towards a strategic emphasis on harnessing data to make substantial advancements in the digital arena.
Giving wings to one’s business in turbulent skies seems to be the mantra for the CIO of Lufthansa Cargo AG - Jochen Gottelmann. He speaks about how Lufthansa Cargo responded to the pandemic with agility and resilience, and how LTIMindtree helped drive it’s ESB middleware transformation. In Jochen’s words, LTIMindtree has proven to be a reliable, competent, scalable & trustworthy partner – both, in good times and in not so good times.
David Johnston, CIO of Messer Americas talks about their digital transformation and how LTIMindtree has played a key role to bring technology leadership and innovations.
Mr. Stavros Ioannou, Deputy CEO, Group COO & International Activities, highlights that their partnership with LTIMindtree enables them to deliver IT services aligned with their customers’ needs, no matter where they are.
Béatrice Mabille, VP Internal IT of Criteo discusses the indispensable support of LTIMindtree to reach their objectives: cost efficiency operating model, a strong reliability to have time to focus on the projects and maximizing the value.
LTIMindtree played a pivotal role in evaluating risks and ensuring a successful migration within budget and schedule. Post-acquisition, AMBA flourished, serving over 450 affinity groups with an expanded product portfolio
LTIMindtree played a pivotal role in Gen Re's cloud migration journey, addressing scale challenges and geographic diversity with a highly skilled team. Their comprehensive approach ensured a seamless transition, meeting Gen Re's objectives successfully. Erik Kasir, VP at Gen Re, commended LTIMindtree for their strategic selection, effective risk mitigation, and collaborative teamwork.
Johan Gabrielsson, Head of Digital Products & Services at OKQ8, talks about their long-lasting partnership with LTIMindtree in Digital Products & Platforms. The association has expanded from early IT development to creating innovative apps for sustainable mobility. OKQ8 and LTIMindtree's partnership has now shifted towards a strategic emphasis on harnessing data to make substantial advancements in the digital arena.
Giving wings to one’s business in turbulent skies seems to be the mantra for the CIO of Lufthansa Cargo AG - Jochen Gottelmann. He speaks about how Lufthansa Cargo responded to the pandemic with agility and resilience, and how LTIMindtree helped drive it’s ESB middleware transformation. In Jochen’s words, LTIMindtree has proven to be a reliable, competent, scalable & trustworthy partner – both, in good times and in not so good times.
David Johnston, CIO of Messer Americas talks about their digital transformation and how LTIMindtree has played a key role to bring technology leadership and innovations.
Mr. Stavros Ioannou, Deputy CEO, Group COO & International Activities, highlights that their partnership with LTIMindtree enables them to deliver IT services aligned with their customers’ needs, no matter where they are.
Béatrice Mabille, VP Internal IT of Criteo discusses the indispensable support of LTIMindtree to reach their objectives: cost efficiency operating model, a strong reliability to have time to focus on the projects and maximizing the value.
LTIMindtree played a pivotal role in evaluating risks and ensuring a successful migration within budget and schedule. Post-acquisition, AMBA flourished, serving over 450 affinity groups with an expanded product portfolio
LTIMindtree played a pivotal role in Gen Re's cloud migration journey, addressing scale challenges and geographic diversity with a highly skilled team. Their comprehensive approach ensured a seamless transition, meeting Gen Re's objectives successfully. Erik Kasir, VP at Gen Re, commended LTIMindtree for their strategic selection, effective risk mitigation, and collaborative teamwork.
Success Stories
Recognitions
LTIMindtree achieves Indirect Supplier of the Year Award 2024 at Carrier Global Supplier Summit. The award highlights LTIMindtree's dedication, excellence, and trusted partnership with Carrier.
Read More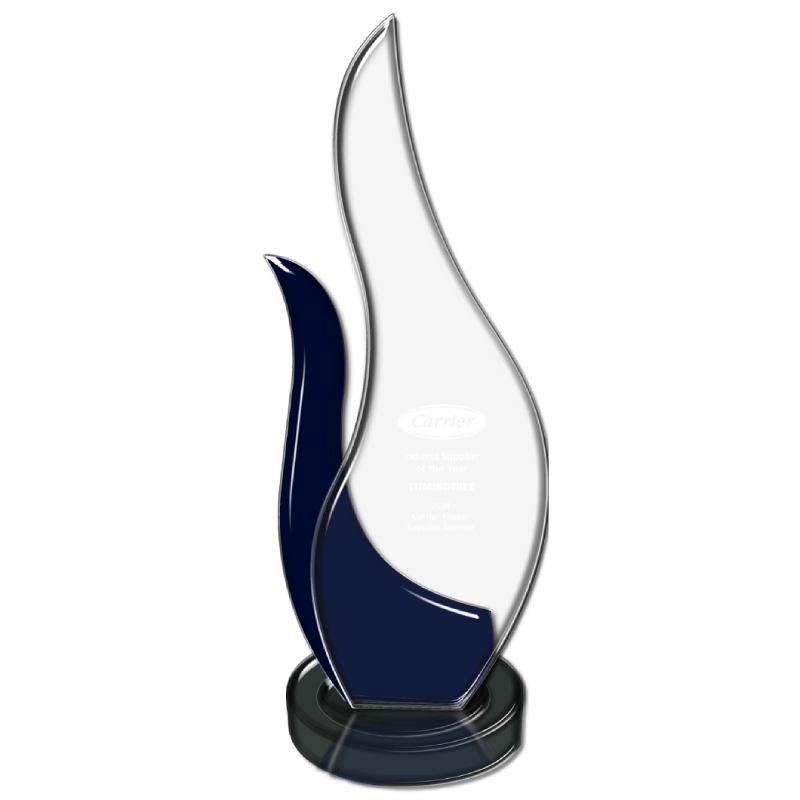
Recognitions
LTIMindtree has been awarded the prestigious nasscom Spotlight Award for Best-in-Class R&D Organization! The Spotlight Awards recognizes organizations that are making significant contributions to the Research & Development landscape.
Read More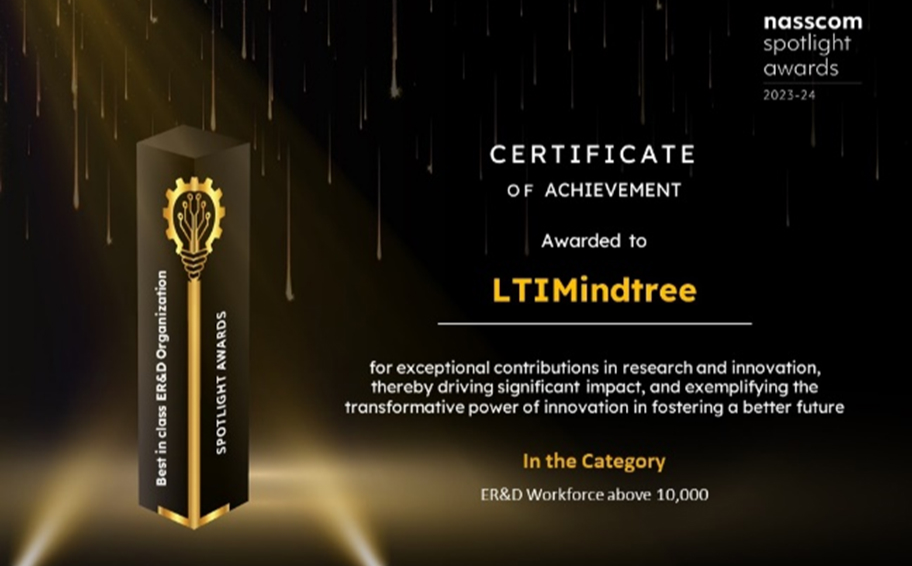
Recognitions
LTIMindtree recognized as a Great Place to Work in Poland
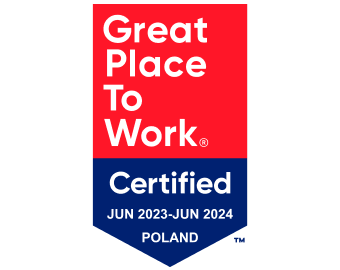
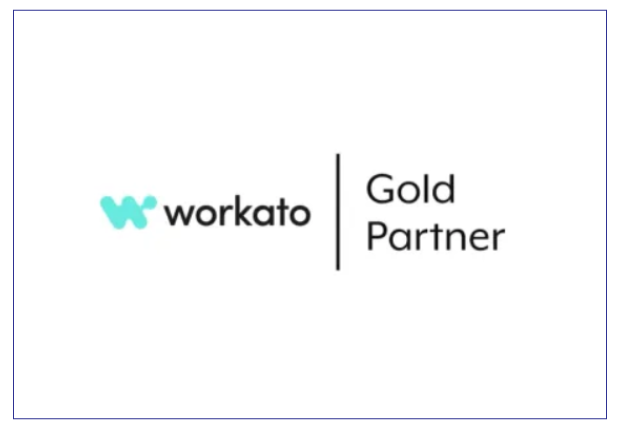
Recognitions
A Hat Trick of Honors: LTIMindtree Wins Three Prestigious Awards at The LACP Annual Sustainability Report Competition Vision Awards, 2023-24
Read More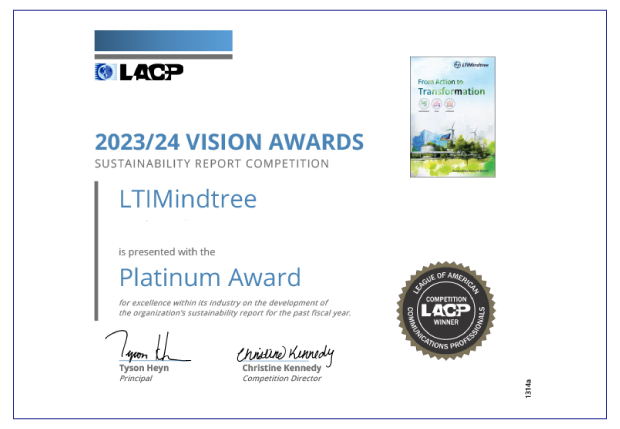
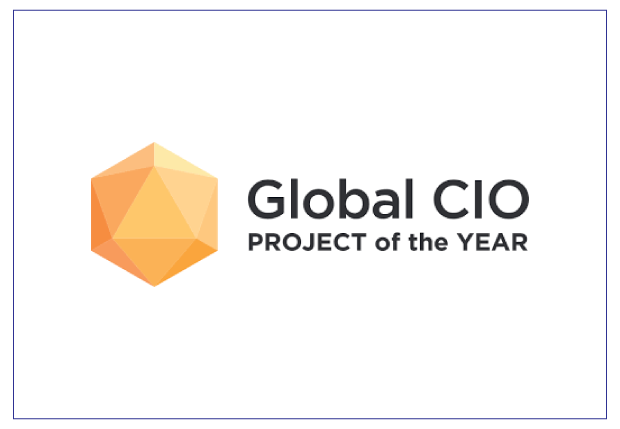
Recognitions
LTIMindtree achieves Indirect Supplier of the Year Award 2024 at Carrier Global Supplier Summit. The award highlights LTIMindtree's dedication, excellence, and trusted partnership with Carrier.
Read More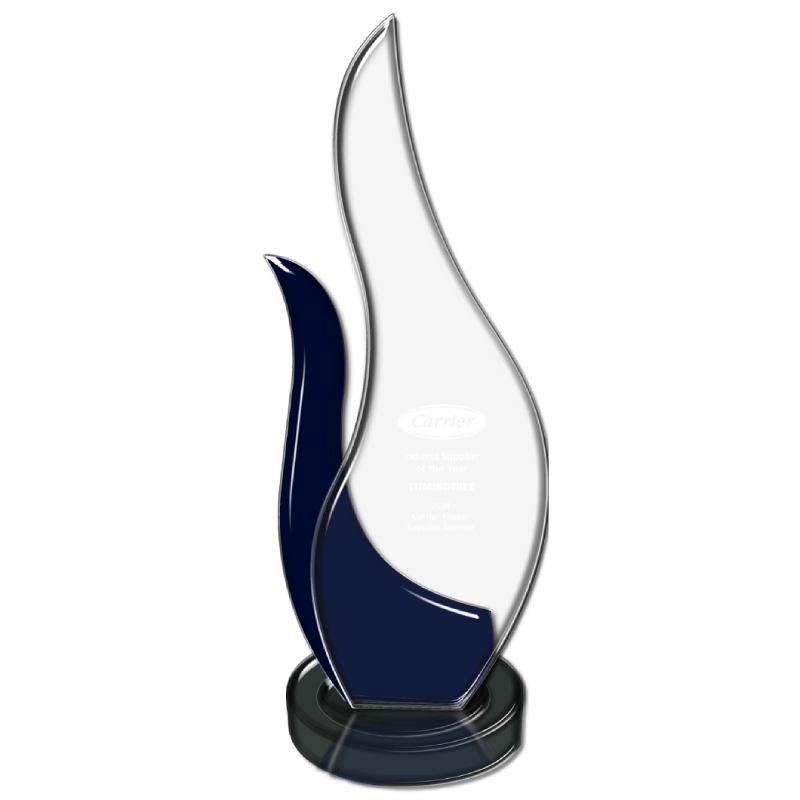
Recognitions
LTIMindtree has been awarded the prestigious nasscom Spotlight Award for Best-in-Class R&D Organization! The Spotlight Awards recognizes organizations that are making significant contributions to the Research & Development landscape.
Read More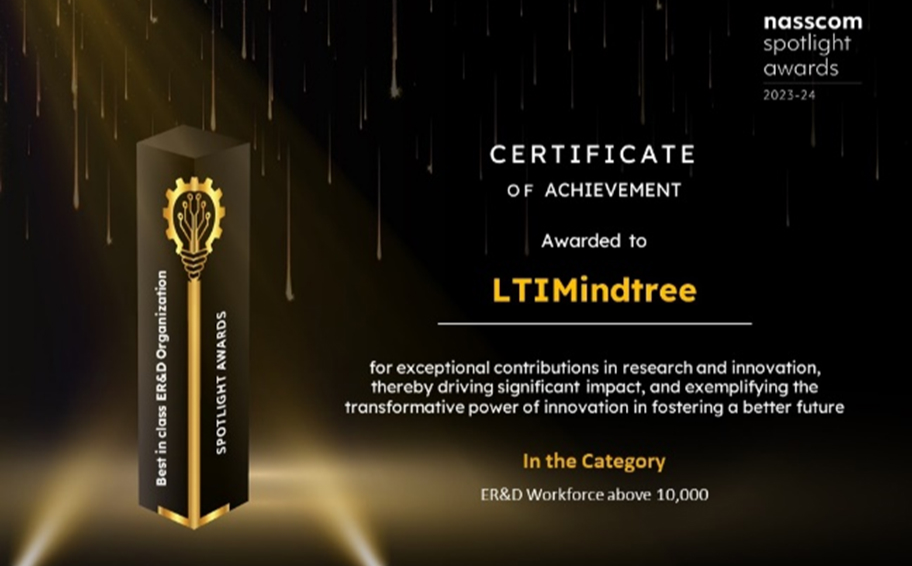
Recognitions
LTIMindtree recognized as a Great Place to Work in Poland
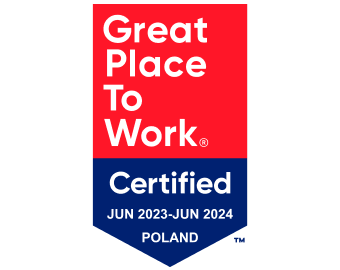
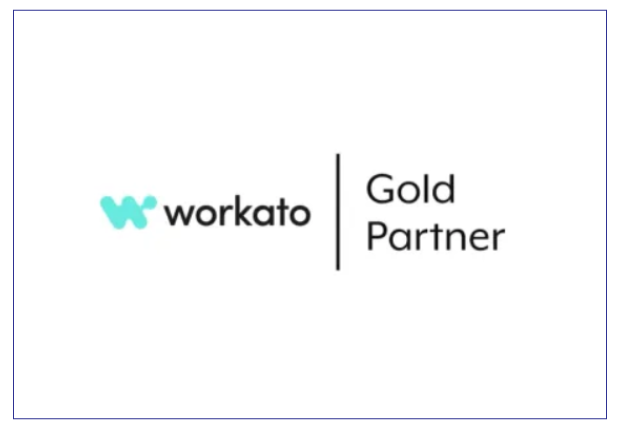
Recognitions
A Hat Trick of Honors: LTIMindtree Wins Three Prestigious Awards at The LACP Annual Sustainability Report Competition Vision Awards, 2023-24
Read More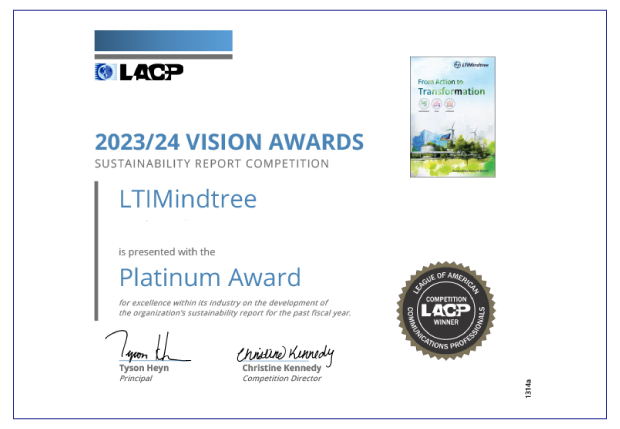
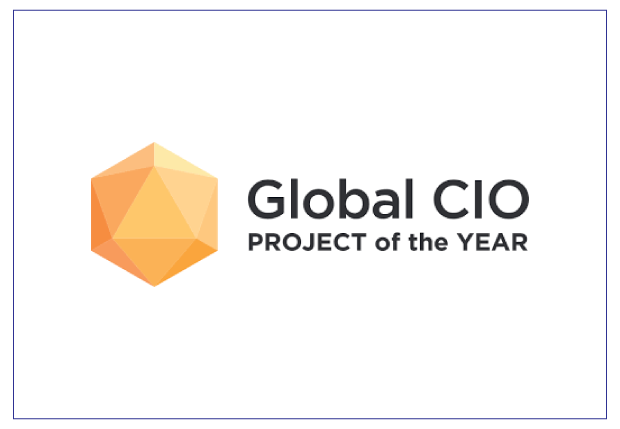