Client
A major energy solutions provider took a significant step toward decarbonizing industrial processes by establishing a Green Hydrogen plant focused on clean and sustainable innovations. Powered by solar-generated electricity, the plant produces hydrogen through electrolysis, a clean process that separates water into hydrogen and oxygen. This hydrogen production supports critical operations at an adjacent heavy engineering complex, fueling welding and heat treatment processes. In turn, this contributes to the facility’s sustainable energy goals through smart energy Management Systems.
Key Features of the Green Hydrogen Plant
- Efficient hydrogen production: The facility employs advanced electrolysis technology with digital systems for real-time monitoring and optimization and predictive maintenance.
- Capacity and scalability: The plant is designed to dynamically adjust production capacity based on demand from the adjacent heavy engineering complex.
- Renewable energy integration: The space is integrated with renewable energy sources, ensuring that hydrogen production remains eco-friendly and fully aligned with innovation in renewable energy efforts.
- Sustainability contribution: The project significantly contributes to India’s goal of achieving net-zero emissions by 2070. By providing a green alternative to conventional hydrogen production, it helps reduce reliance on fossil fuels and supports the decarbonization of hard-to-abate sectors.
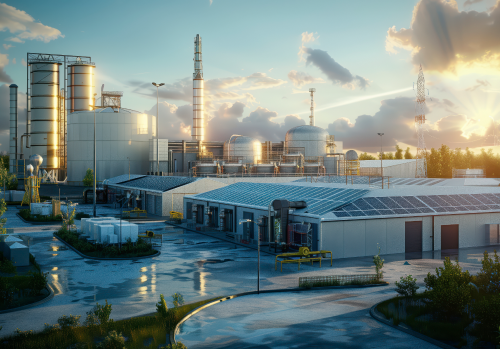
This initiative marks a crucial step in advancing clean energy practices while positioning India as a leader in smart energy management systems.
Market Trends in Green Hydrogen Production
The global green hydrogen market is expanding rapidly, valued at $7.98 billion in 2024, with an expected CAGR of 38.5% from 2025 to 2030. Technological advancements in proton exchange membrane (PEM) and alkaline electrolyzers are making electrolysis more cost-effective, increasing green hydrogen’s competitiveness with traditional energy sources. Major economies like Europe and the US are investing in localized electrolyzer manufacturing to reduce import reliance and strengthen domestic supply chains.
Industries that are difficult to electrify—such as steel, cement, and chemicals—are integrating green hydrogen to lower carbon emissions, while the transportation sector is exploring hydrogen fuel cells as an alternative to diesel and jet fuel. However, scaling production remains challenging due to high energy demands, operational inefficiencies, and the need for real-time monitoring. To stay competitive, energy firms must optimize production, minimize downtime, and integrate intelligent systems to enhance efficiency and long-term sustainability.
Challenges
Despite its significant achievements, the Green Hydrogen plant faces several operational and technological challenges that could impact efficiency, safety, and sustainability.
Operational challenges
- A lack of real-time data on hydrogen production, energy consumption, and equipment performance hinders optimal resource utilization.
Maintenance challenges
- Unplanned downtime: Without prediction maintenance systems, unexpected equipment failures can lead to costly disruptions.
- Increased maintenance costs: Reactive repairs and frequent equipment breakdowns increase expenses and reduce the plant's profitability.
- Longer troubleshooting times: Identifying and resolving issues without real-time diagnostics takes significantly longer, delaying restoration of normal operations.
Safety and risk challenges
- Safety risks: Without predictive maintenance systems, unexpected equipment failures can lead to costly disruptions.
- Delayed response to anomalies: The absence of real-time monitoring limits the ability to address issues promptly.
Process optimization challenges
- Limited real-time insights: Absence of data-driven decision-making results in inefficiencies in scaling operations or modifying processes.
- Restricted remote access: Operators and engineers cannot access plant data remotely, thereby increasing the need for their physical presence on-site.
Sustainability challenges
- Energy wastage: Green hydrogen production is energy intensive. Without real-time monitoring, energy losses during electrolysis or renewable energy integration may go unnoticed.
Transformation Journey
To overcome operational challenges and enhance efficiency, a comprehensive digital transformation was undertaken at the newly established Green Hydrogen plant in India. Spearheaded by LTIMindtree’s iNXT, the initiative focused on leveraging advanced technologies to optimize hydrogen production, ensure operational precision, and enable real-time decision-making.
Key Highlights
Our Solution
We collaborated with the client as their consulting and engineering partner to define their transformation journey.
Key steps included:
Conclusion
By integrating smart energy management systems and driving innovation in renewable energy, the Green Hydrogen plant exemplifies a successful transformation toward sustainable and efficient industrial processes. The strategic deployment of AI-driven insights and scalable architectures enabled the client to overcome operational challenges, optimize resources, and contribute meaningfully to India’s net-zero goals.
Ready to modernize your green energy operations? Contact us at https://www.ltimindtree.com/inxt/.
Let’s build a sustainable future together!